Business Process Optimization: Strategies to Improve Efficiency and Effectiveness of Modern Companies.
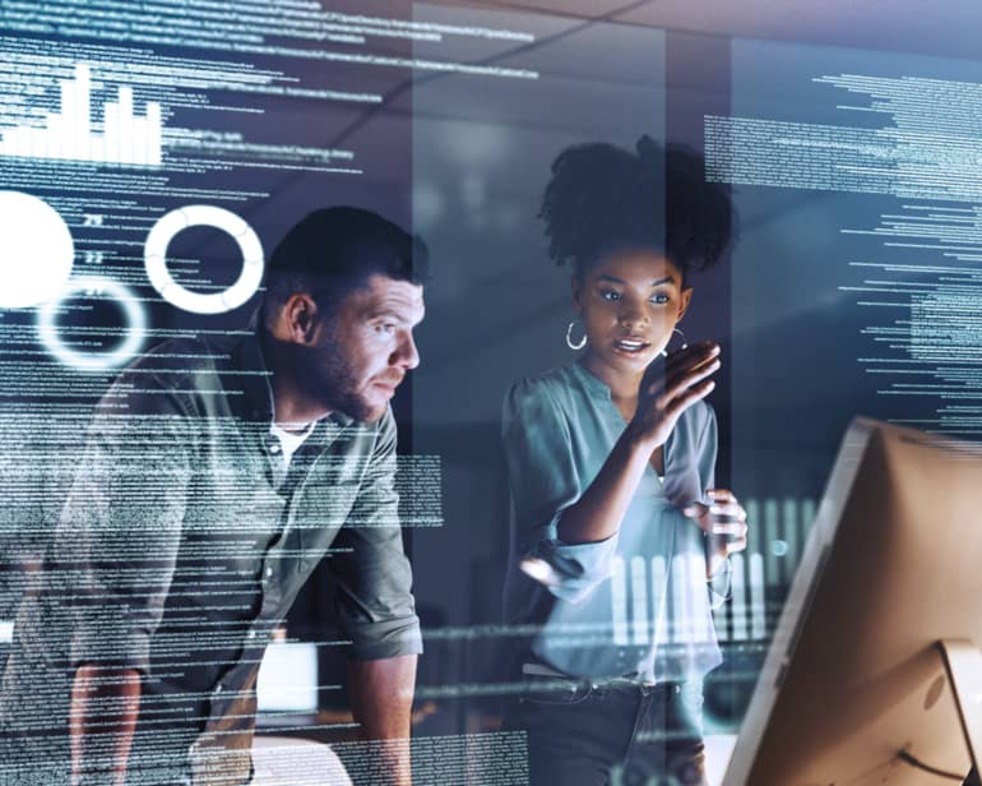
In today’s fast-paced business environment, companies are constantly seeking innovative strategies to optimize operations and improve efficiency and overall effectiveness. As companies face increasing pressure to reduce operational waste and remain competitive, the need to streamline processes has become critical. A key way to achieve this is to leverage advanced technology to automate repetitive tasks, which not only speeds up operations but also minimizes human errors.
In addition, process mapping is an important tool for identifying inefficiencies, allowing companies to visualize workflows and implement targeted improvements. Lean management techniques, based on the principle of focusing on value creation while minimizing waste, have gained traction in various fields, including the service industry, but their adoption has often been met with resistance due to cultural and structural challenges.
Improving employee productivity is equally important, and cultivating employee engagement through targeted strategies and strong training and development programs can significantly improve operational performance. A positive work culture further increases productivity and creates an environment that motivates employees to contribute to company goals. In addition, integrating data analytics into the decision-making process has proven to be a powerful driver of operational excellence. It not only supports intelligent decision-making, but also provides companies with effective data and predictive analysis tools to predict trends and prepare for market changes.
Finally, incorporating sustainable practices into business operations is gaining acceptance not only for its ability to reduce costs but also for its potential to improve brand reputation in a market where corporate responsibility is increasingly valued. However, the path to sustainability also comes with its own challenges, from initial implementation costs to stakeholder resistance. In this article, we examine these multifaceted strategies for optimizing business operations and provide a comprehensive analysis of the methods, benefits, and barriers associated with improving efficiency and effectiveness in modern organizations.
Strategies for Streamlining Processes
What are the main ways to reduce operational waste?
Reducing operational waste is a multifaceted challenge that can be effectively addressed through several key strategies. One of the most important methods is to standardize processes to ensure consistent and efficient operations and minimize waste. By adopting a set of standardized procedures, companies can reduce operational variations that often lead to inefficiencies and waste. In addition, regular process reviews are also important because they allow companies to identify specific areas where waste can be reduced.
These reviews may result in process steps being rearranged, which is also an effective waste reduction strategy. In addition, continuous improvement through regular training is essential because it improves the skills and knowledge of employees and ensures that operators are well trained and equipped to remain efficient. This not only helps with individual development, but also ensures that employees can meet and maintain established standards and minimize waste.
The combination of these approaches provides a powerful framework for reducing operational waste and highlights the importance of a properly configured and skilled workforce in achieving sustainable efficiency.
How can we leverage technology to automate tasks?
Automation through the strategic use of technology offers the opportunity to significantly improve operational efficiency across sectors. For example, the banking industry has successfully used robotic process automation to automate repetitive tasks, demonstrating the potential to streamline operations and reduce the need for human intervention. This success can serve as a blueprint for other industries, such as healthcare and manufacturing, where RPA is less common but still very promising. By assessing the processes that cause operational waste, these industries can identify specific tasks that are suitable for automation, ultimately improving efficiency and resource management. In addition, a well-structured research program will guide the exploration of future directions for automation and ensure the best use of technological advances.
This proactive approach is essential to harnessing the power of technology to automate tasks and optimize productivity and resource utilization across industries. Expanding these efforts to other industries will unlock a wealth of untapped opportunities and promote a more efficient, technology-integrated operating environment. Therefore, the targeted, strategic use of technology to automate tasks can significantly improve operational efficiency and reduce costs. All sectors have waste.
What role do flowcharts play in identifying inefficiencies?
Continuing with the discussion on the use of technology, flowcharts have proven to be an important tool for identifying inefficiencies in workflows. By using tools such as value stream mapping and simulations to visually represent current processes, companies can identify areas plagued by waste, delays, and potential improvements, providing clear paths for improvement. This analytical approach provides a deeper understanding of task sequencing, roles, and stakeholder interactions, which can then be optimized to streamline operations and eliminate redundancies.
Companies can use insights from flowcharts to redesign workflows to improve efficiency and effectiveness and align them closely with strategic goals. Integrating flowcharts into the operational toolkit not only allows companies to improve immediate processes, but also lays the foundation for continued innovation and adaptability in an increasingly competitive environment. As mentioned above, a deliberate focus on flowcharts can greatly aid in achieving automation goals by providing a structured approach to refining and improving workflows prior to automation.
Implementation of Lean Management Techniques
What are the principles of Lean Management?
At its core, Lean Management is the principle of cross-departmental efficiency, which aims to streamline processes by improving collaboration and communication between different departments within a company. This principle is closely related to improving workplace efficiency because it promotes a holistic understanding of company processes and ensures that all functions are aligned with overall goals.
A key element in achieving this cross-departmental synergy is a comprehensive training program, including: B. "5S" training. It provides employees with the skills and knowledge needed to identify and eliminate inefficiencies. The emphasis on teamwork further supports these efforts by promoting customer-supplier logic and encouraging departments to work seamlessly together to provide value to the end customer. Through these strategies, lean management not only improves productivity, but also enables organizations to remain flexible and respond quickly to market changes. This ultimately requires a culture of continuous improvement and proactive problem solving.
How can lean techniques be applied to the service industry?
Incorporating lean techniques into the service industry requires a comprehensive approach that takes into account the unique challenges of these industries.
Industry. For example, reducing delivery time is an important aspect of improving service efficiency. After adopting lean practices, meal preparation time was reduced by 55%, highlighting the potential for improved customer satisfaction and operational efficiency.
In addition, implementing lean management can significantly reduce overall costs. Some service industries have reduced spending by 16%, highlighting the economic benefits of implementing lean techniques. An important part of this approach is employee empowerment, supported by training programs such as TWI, which enables employees to work more autonomously and efficiently.
This improvement not only reduces the need for oversight, but also enables business owners to focus on strategic, non-operational activities, fostering a more innovative and agile business environment. By focusing on these key areas, service industries can effectively leverage lean techniques to drive operational improvements and provide greater value to customers.
What are the most common challenges when implementing lean management?
While technological advances such as RPA have the potential to automate tasks, implementing lean management faces unique challenges rooted in organizational culture and human factors. One of the biggest challenges is the lack of time companies face, as both employees and management struggle to find the time needed to effectively implement lean management practices.
The majority of manufacturing companies, including 20% of lumber companies, say they lack the time to implement these practices, a persistent problem across the industry. While senior management and team leader involvement is critical to lean implementation, many companies do not provide adequate support, exacerbating the problem. This lack of support is often related to a lack of financial resources or the need for a clear vision, which can complicate the process of lean implementation.
Additionally, cultural change is a major barrier, requiring commitment and leadership from senior management to lead by example and achieve the necessary changes in behavior, culture, and attitudes. These links between lack of time, resource allocation, and cultural barriers highlight the complexity of implementing lean management, and successfully overcoming these challenges requires a systematic approach and strong leadership.
Improving Employee Productivity
What strategies can improve employee engagement and productivity?
To effectively improve employee engagement and productivity, companies must implement comprehensive strategies that consider the various factors that influence employee performance. One key strategy is to focus on leadership and capability development. This plays a key role in improving engagement and productivity by providing guidance and creating a supportive work environment.
In addition, it is important to develop effective training and development programs because these initiatives not only improve engagement, but also equip employees with the skills they need to complete tasks effectively, thereby improving overall productivity. Another strategic approach is to encourage open and continuous communication between managers and employees.
This is important to create an environment where employees feel valued and heard, thereby increasing engagement and motivation. In addition, rewards and recognition are also powerful motivators because they recognize employees' contributions and encourage them to maintain high levels of performance. By integrating these strategies, companies can create a more engaged and productive workforce, ultimately contributing to long-term success and market competitiveness.
How does training and development improve operational efficiency?
Training and development plays a key role in further improving operational efficiency by providing employees with the skills they need to reduce waste and optimize processes.
Developing a comprehensive training program is important for an effective operational strategy. The example of a Ghanaian company shows that such a strategy can help improve workflow and reduce waste. Furthermore, companies that invest in training and development see high productivity and high-quality performance as essential to maintaining a competitive advantage.Training programs that focus on strategic planning and goal setting teach employees key business skills, align their efforts with organizational goals, and improve operational efficiency.
Furthermore, fostering a collaborative environment where employees can voice their concerns and offer their ideas fosters innovation and collaboration, improving overall operational efficiency. These interrelated factors highlight the importance of training and development to improve operational efficiency and the need for continuous investment in employee skills and support infrastructure to maintain progress and adapt to changing operational needs.
How does corporate culture impact productivity?
The impact of organizational culture on productivity is complex and extends beyond technology adoption to the broader corporate environment in which employees work. A positive corporate culture is essential to foster employee innovation, a key driver of productivity.
Such a culture not only fosters creativity, but also enhances, sustains, and motivates employee performance, ensuring that company goals are efficiently achieved. Furthermore, since knowledge professionals often lead innovation within organizations, their perception of innovation in the workplace is a key factor in understanding the impact on productivity. In this context, a high level of trust between employees and organizations has proven to be a fundamental element for building an environment that fosters productivity and innovation. Therefore, maintaining a collaborative and constructive corporate culture is crucial as it can significantly improve employee retention and contribute to the long-term success of the company.
Adopting an employee-centric approach allows policymakers and management to improve the corporate culture, which ultimately increases productivity and ensures the company's competitive advantage in the global market.
Using Data Analytics to Make Decisions
How can data analytics improve operational decisions?
The integration of data analytics into operational decision-making processes has significantly improved the quality and efficiency of decisions within organizations. At the heart of this transformation is big data analytics, which has proven to be a key factor in generating meaningful insights that help improve decision-making quality.
Leveraging BDA capabilities allows organizations to access extensive data resources to generate data-driven insights that act as a mediator between these capabilities and improved decision-making quality. This process is further supported by business intelligence and analytics that rely entirely on such insights to provide relevant and actionable information for improving operational decisions. These data-driven insights strengthen the positive relationship between BDA capabilities and decision-making quality, thus enabling companies to better make informed strategic decisions that drive performance and innovation. Despite the clear benefits, the specific mechanisms by which BDA impacts decision quality require further study to fully realize its potential in different operational environments.
With data analytics playing a central role, companies must continue to invest in and evolve their data capabilities to stay competitive and keep up with the dynamic business environment.
Which tools are essential for effective data analysis in your operations?
To optimize business operations and improve decision-making, it is essential to integrate advanced data analytics tools, especially when dealing with complex big data. Business intelligence tools combined with big data analytics are the basis for transforming raw data into actionable insights. This allows companies to generate detailed reports and conduct in-depth data investigations.
These tools not only support efficient processing of data but also enable companies to adapt to changing market demands through on-demand interactions with data service providers. These capabilities are critical for industries such as telecommunications and healthcare, which rely heavily on advanced analytics to maintain a competitive advantage.
Moreover, as the volume and variety of data continues to grow, there is an urgent need for a powerful and highly scalable data processing infrastructure that can effectively manage and analyze this data. Therefore, for companies looking to leverage big data for performance and strategic advantage, investing in these advanced analytical tools and infrastructure is essential to remain resilient and adaptable even in a rapidly changing data environment.
How can I use predictive analytics to forecast business trends?
Based on the transformative potential of automation technologies, predictive analytics has emerged as a key tool for forecasting business trends, thereby delivering competitive advantage in multiple sectors. By integrating advanced data mining techniques, companies can gain valuable insights from large data sets and forecast future trends that drive strategic planning. This approach is particularly beneficial in sectors such as finance and marketing, where predictive analytics has proven highly effective in developing business strategies that respond to changing market dynamics.
Furthermore, the use of predictive modeling techniques allows for a more informed decision-making process, allowing companies to not only predict customer behavior, but also allocate resources more effectively to improve ROI.
Combining AI algorithms with predictive analytics further improves the ability to analyze large, complex datasets, allowing companies to gain actionable insights that are essential for accurate business forecasting. Recognizing that these technologies and methodologies go hand in hand, it highlights the need for companies to adopt predictive modeling best practices to be agile and respond to emerging trends in an increasingly data-driven market.
Integrating sustainable practices into your operations
What sustainable practices can reduce operational costs?
As the various strategies for improving environmental performance and operational efficiency show, integrating sustainable practices into operational processes can significantly reduce costs. For example, using reusable racks to deliver materials directly to the assembly line not only improves system performance but also reduces delivery times, directly contributing to reduced operational costs. In addition, adopting sustainable packaging solutions, such as eco-friendly and reusable options, can have a positive impact on business performance by minimizing damage to products during transportation and reducing costs associated with returns and exchanges.
Beyond packaging, it is also important to develop a mutual understanding with suppliers about environmental responsibility. This leads to improved operational efficiency and supply chain performance, which in turn leads to cost savings. These interrelated practices highlight the importance of a holistic approach to sustainability, where everything from packaging to supplier collaboration plays a key role in achieving cost-effective operations. To maximize these benefits, companies must actively participate in and maintain ongoing environmental programs and work with suppliers to ensure all parties are aligned toward common sustainability goals.
How do sustainable practices improve brand reputation?
For companies looking to improve their brand reputation, incorporating sustainable practices into their sourcing decisions is a critical step. Companies that incorporate sustainability into their sourcing are not only focusing on operational performance objectives such as quality, reliability, and flexibility, but they are also positioning themselves as responsible companies in the eyes of consumers. This alignment is crucial as it helps to mitigate reputational risks associated with the supply chain.
Reputational risks, if left unmanaged, can lead to serious economic and financial problems, including reputation damage. By prioritizing sustainable procurement, companies can improve their procurement and supply management performance, which in turn has a direct positive impact on brand reputation.
In addition, embedding a culture of sustainability into a company's core values can significantly improve operational efficiency and help build a positive perception of the brand. Thus, incorporating sustainable practices into procurement not only supports operational goals, but also strengthens the company's reputation among stakeholders, forcing them to adopt these practices to protect and enhance their brand reputation.
What challenges do you need to overcome when implementing sustainability in your company?
The implementation of sustainability in operations is a multifaceted challenge that requires the development of new capabilities and the integration of sustainability into the overall business strategy. This integration is not easy, as sustainability goals must be aligned with existing metrics.
This can be difficult, as traditional performance management systems often cannot achieve new sustainability goals. In addition, companies must address sustainability challenges throughout their value chains and operational networks, and must comprehensively reassess their operational frameworks to ensure compliance with sustainability principles. A fundamental aspect of this challenge is to expand the boundaries of operational management to incorporate a sustainability-based approach, which requires a redefinition of traditional operational boundaries.
This expansion requires not only technical and organizational adjustments, but also a shift in corporate philosophy towards a comprehensive sustainability approach. This highlights the need for companies to go beyond basic compliance and pursue innovative and socially responsible management strategies that truly embody sustainable practices. To achieve true sustainability, companies must not only meet minimum requirements for environmental, social and economic factors, but also pursue additional goals that are consistent with target groups and market conditions. Addressing these challenges is therefore essential for companies that want to effectively realize sustainability and ensure that their operations contribute to environmental protection and social justice.
Conclusion
The findings of this study highlight the important role that strategic automation and integration of sustainable practices can play in optimizing operations for modern companies. It is widely acknowledged across all industries that companies can significantly improve operational efficiency and reduce waste through the use of technology. To achieve this efficiency, a focus must be placed on well-trained employees, as regular training not only equips employees with the necessary skills but also promotes a culture of continuous improvement.
In addition, the value of standardized processes cannot be overstated. They are a means of minimizing variability and ensuring operational consistency and reliability. However, incorporating sustainability into operational frameworks is a complex challenge that requires a reassessment of existing metrics and performance management systems. The study highlights the importance of aligning sustainability goals with organizational goals, which requires a change in corporate philosophy and operational strategy.
While significant progress can be made through approaches such as lean management and process mapping, companies must also overcome unique challenges, such as time constraints and the need for cross-functional collaboration. The study identifies and raises gaps in the current understanding of how to effectively integrate sustainability efforts into the value chain.
Further research is needed in this area. In addition, the potential of big data analytics to support decision-making and improve operational efficiency provides a starting point for future research, particularly to understand how data-driven insights mediate the relationship between operational capabilities and performance outcomes.
As companies seek to remain competitive in a rapidly evolving business environment, the findings of this article advocate for a holistic approach that emphasizes not only efficiency and effectiveness but also sustainability as a fundamental business principle. Ultimately, this discussion contributes to the ongoing dialogue about optimizing business practices by highlighting the interconnectedness of technology, workforce development, and sustainability in driving operational excellence.